Aluminium Alloy Capacitor Discharge Weld Studs M8x 30mm Length
Shipping options
Find a local distributer
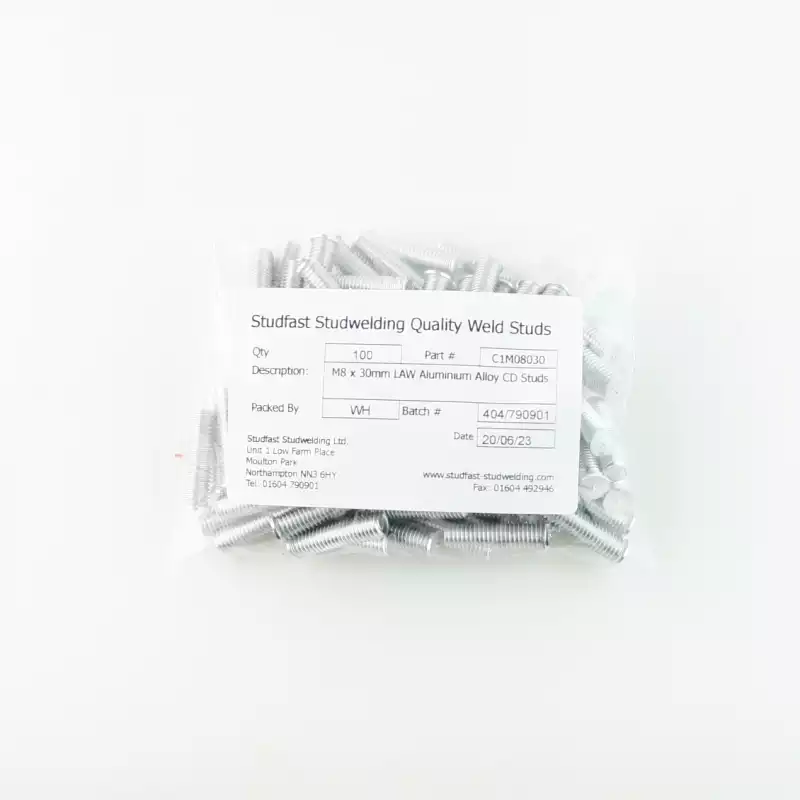
Aluminium Alloy Capacitor Discharge Weld Studs M8x 30mm Length
General specs
- Material:Mild Steel Copper Coated
- Manufacturing Certification:ISO 13918
- Threading Spec.:M8
- Threading compatibility:Metric Standard
Pip Length Specifications
- The pip on the end of the stud is the timing mechanism for the entire weld. As such we are militant about testing all our studs to ensure not only apparent physical consistency, but also consistency in the welds they produce.
- Length of Pip:1mm target length (We determine accepted variance by testing)
- Pip Diameter:0.5mm with 0.012mm variance - (between 0.588 and 0.612mm)
The Studfast ISO 13918 Capacitor Discharge Studwelding Stud Specification Drawing
Our drawing available below clearly illustrates the key dimensions essential for consistent, quality welds. Our drawing is created with clarity in mind overviewing the key factors in the ISO specification. Should you require an exhaustive CAD drawing of the exact spec, just fire us an email and we will provide one for you.
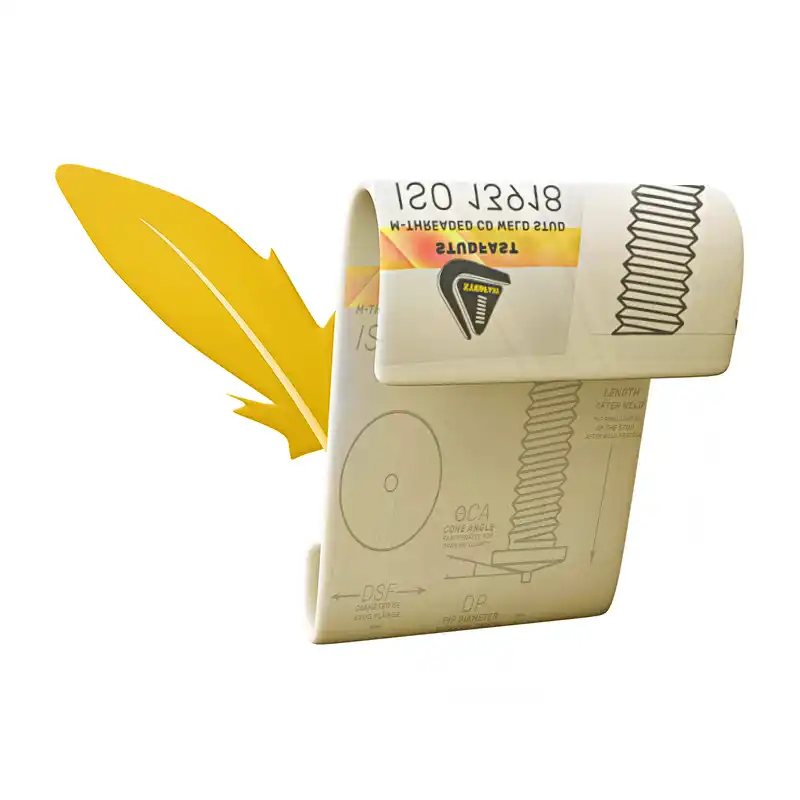
Download the The Studfast ISO 13918 Capacitor Discharge Studwelding Stud Specification Drawing here. Just click the button above. Should you require an alternative format, please don't hesitate to send us an email.
Stud Length Characteristics
- Our stud length specifications are measured as LAW meaning 'Length after Weld'. This is because during the weld process some of the parent material is blown away as weld spatter, (albeit minimal for the CD process.) Also some of the material is turned to plasma and a further volume of the material is liquified, filling the weld cavity and moving to the edges of the stud. What we are looking for in a good quality weld is a uniform 'witness' of a minimal solidified molten metal ring around the edges of the stud flange. Later we will discuss cone angle which is there to help this process.
- Stud Length: 30mm LAW (Length After Weld)
- Accepted VariancePlus or minus 0.6mm
- Should you be getting LAW Length After Weld measurements exceeding this variance then that would indicate a problem in setup. Call our experienced team and we will be there to help you rectify any issues, free of charge. Calibrate customers also benefit from unlimited preferential 24/7 support, on site visits or virtual troubleshooting over Zoom (preferred), Skype or Facetime
Weld Specific Attributes (as detailed on our ISO 13918 drawing)
- The Studfast ISO 13918 Capacitor Discharge Studwelding Stud Specification Drawing illustrates some design features that must be stringently controlled to ensure quality welds. Firstly, while the end of the stud may look flat to the naked eye, there is in fact a shallow angle causing the pip to protrude further out, giving a conical end. This design feature is essential to ensure the weld pool that begins vaporising and liquifying at the centre, is evenly worked outward during the weld, aided by the spring pressure in the weld head or hand tool.
- Angle Marked 'ΘCA' (for Cone Angle):2.2 degrees to 3.8 degrees
- N.B.// This Cone Angle is greatly exaggerated in our drawing to illustrate its existence and make it clear what the 'ΘCA' placeholder is referring to
Certificate of Conformity
- Your online purchase includes a Certificate of conformity. This will be emailed to you immediately upon your purchase. Metallurgy certificates and other supporting documentation is available upon request. Ideally shoot us an email, (received directly by our technical team,) or call our main line and speak to a human immediately, (no frustrating voice menus,) who will be able to deal with your request 24/7.
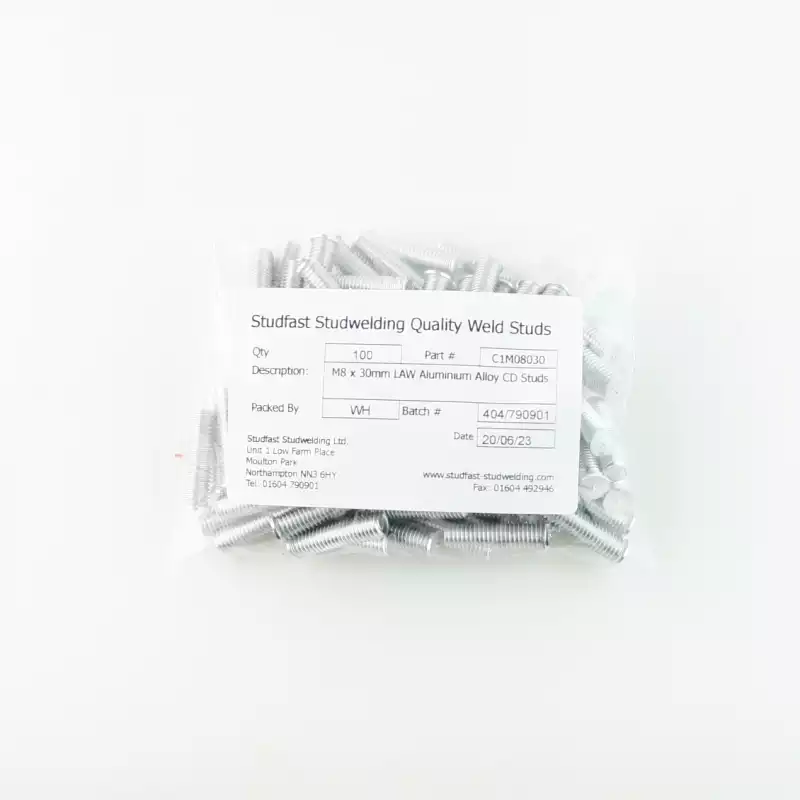
Aluminium Alloy Capacitor Discharge Weld Studs M8x 30mm Length
( ! ) Notice: Undefined variable: reviews in /var/www/www.studfast-studwelding.com/shop/aluminium-alloy-welding-studs-thread-metric-cd-fasteners/index.php on line 793
Call Stack
# Time Memory Function Location
1 0.0001 361592 {main}( ) .../index.php:0
Reviews
3.6 Overall rating
36 out of
(69%)( ! ) Notice: Undefined variable: reviews in /var/www/www.studfast-studwelding.com/shop/aluminium-alloy-welding-studs-thread-metric-cd-fasteners/index.php on line 795 Call Stack # Time Memory Function Location 1 0.0001 361592 {main}( ) .../index.php:0
Customers recommended this product
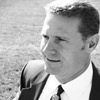
Review from Our Customer by L Clarkson
LeicestershireStudfast are the sort of supplier I like - the parts just arrive when they are supposed to without any issues ,
- Pros: Speedy delivery, always accurate
- Cons: None that I can think of
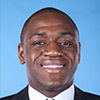
Review from Our Customer by S Rigler,
BasingstokeWe have used Studfast for over 12 years and have always found them to be extremely helpful and very knowledgeable; I would not hesitate to recommend them.
- Pros: Real people, who care about customer service
- Cons: n/a

Review from Our Customer by D Ridgwell,
PortsmouthFantastic quality, expert advice and speedy delivery. Our precision applications demand all these three and in nine years Studfast have never disappointed
- Pros: Product Consistency... this is KEY for us. My previous supplier provided studs with intermittent reliability
- Cons: Did not initially mention ability to schedule orders for volume discount, but that is a minor minor point 🙃
Write a review
Our Other Aluminium Alloy Stud Diameters and Length After Weld (LAW) in mm
We also stock many other exotic sizes and materials of stud, like Brass CD Weld Studs (popular in the engraving industry and with installation artists,) we also have female studs, which are internally tapped so you can screw into them. These are useful for mounting Printed Circuit Boards. If you've got a new project on we're always keen to chat and see if studwelding might be a good fit for your production solution. And we've a plethora of accessories and welding bits and bobs that we haven't had the time to photograph and put in the shop yet, so pick up the
or drop us an if you don't see what you need... and our team'll be back to you in a jiffy : )Our experienced team has been supplying Aluminium Studs to the Engineering Sector Since the Nineteen-Eighties, when it comes to stud welding...
...we know our stuff
Experts in aluminium Stud welding supplies, including aluminium alloy capacitor discharge weld studs, thin diameter aluminium alloy cd weld studs, like M4 threaded AA studs ... we even stock down to 3mm diameter and have M3 threaded weld studs, to the metric pitch specification of thread. We always have some M3 on the shelf ready to go straight out on our orders. As well as aluminium studs, we also sell CD welding equipment. The CD stands for Capacitor Discharge and this is the process most suited to welding metric threaded aluminium cd weld studs. The studs have a tendency to weld extremely fast when working with aluminium alloy, so there is an alternative method to the traditional 'contact' method of cd stud welding and this is called 'The Lift Gap Method'.
Aluminium Alloy CD Weld Studs MUST be "Headed" Correctly to ensure the timing of the Weld is Consistent. Stud Quality and Consistency is Paramount!
Aluminium Stud welding supplies, including aluminium alloy capacitor discharge weld studs, AKA aluminium alloy cd weld studs, some people just say aluminium studs, but aluminium on its own is too soft. We recommend Aluminium Alloy because when the spring pressure is taken up by the welding handtool, sometimes the soft pip on the end of the stud can be crushed and malformed. This sets off the timing of the whole weld. So with the addition of a strengthening alloy, we achieve a tougher stud and are able to more easily achieve consistent weld results. We also sell CD welding equipment. The CD stands for Capacitor Discharge and this is the process most suited to welding metric threaded aluminium cd weld studs. The studs have a tendency to weld extremely fast when working with aluminium alloy, so there is an alternative method to the traditional 'contact' method of cd stud welding and this is called 'The Lift Gap Method'. This innovative process attempts to make up for valuable milliseconds of time lost during the vaporisation of the aluminium allow pip and subsequent liquefaction of the aluminium in the head of the stud.
Mild Steel CD Weld Studs and Stainless Steel Capacitor Discharge Studs do not suffer from this problem. Steel material is obviously a LOT harder than light weight aluminium, and also because of its lower boiling / melting point, we are wanting to use more spring pressure in an Aluminium alloy stud welding to aluminium sheet application.
Welding Aluminium Alloy CD Weld Studs using the Lift Gap process
In aluminium CD weld stud welding using "Lift-Gap", the handtool that houses the aluminium stud within the copper chuck or collet has been modified so that just before the weld takes place the head retracts a little away from the surface. Then at the point of the weld ignition the aluminium stud itself is already moving at speed toward the surface of the job. Now the plasma weld pool can form with greater ease because we are not waiting for weld material to be donated by the stud. In the traditional contact setup the spring in the hand tool would have to be tuned much higher than for welding steel, in order to provide sufficient force to accelerate the body of the stud toward the job as the three degree cone tip leading from the pip which is there by design, is still struggling to bring the metal of the stud together with the surface of the job. This meant sometimes turning up the spring pressure so high that it would sometimes partially crush the comparatively delicate aluminium pip. And as you have probably heard me say before... the pip is critical to the timing of the weld. With the aluminium pip distorted, the entire welding rule-book is effectively thrown out of the window as inherent inconsistencies make it impossible to guarantee a repeatable result
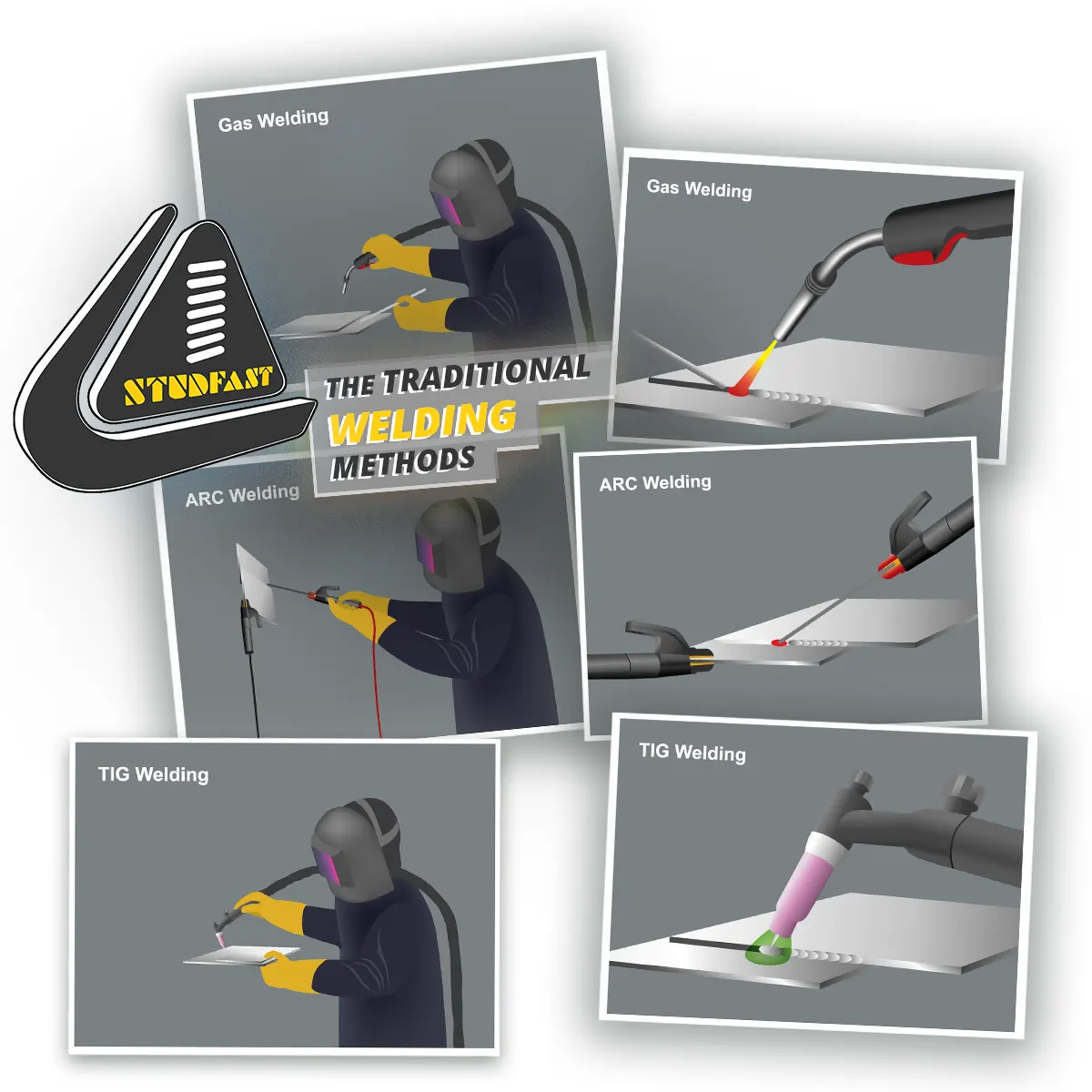
In "The Lift Gap Method" there is no spring pressure because the stud itself is effectively set in motion at the time of the weld and it is this inertia that provides the necessary force which works especially well at the traditionally troublesome lower diameters. Aluminium has kind of got a bit of a bad rep, generally, in the welding industry. It's messy, it spits, it can be dangerous managing the weld with the more technically demanding processes like MIG and TIG. It is not dangerous at all when welded using Capacitor Discharge welding systems, but it can make a bit more of a bang, with more visible bright spatter. And achieving deep penetration into the parent material in order to have a successful weld, means toying around with the settings a bit more than with Steel.
Why would you choose to use aluminium instead of steel for cd stud welding in specific applications?
The several reasons why aluminium may be used instead of steel for capacitor discharge stud welding applications include, weight considerations, electrical and thermal conductivity, corrosion resistance and thermal expansion. But the main reason might just be compatibility, in that if you are trying to achieve a proper weld, (and not just a brazing of two different materials,) you have to use the same material or as close as possible to ensure an even join at the molecular level. A true weld should be stronger than the surrounding material on the job and the stud. This is because in the process of heating up, liquifying and then cooling back down, the crystalline lattice structure of the metal is allowed once again to re-distribute itself, improving its structural uniformity. This is apparent when we use destructive testing to test for weld quality. You would expect to see the stud fail or for it to pull a slug out of the parent sheet metal when exerting angular force on the completed weld. A good weld will never break at the point of contact between the stud flange and the plate.
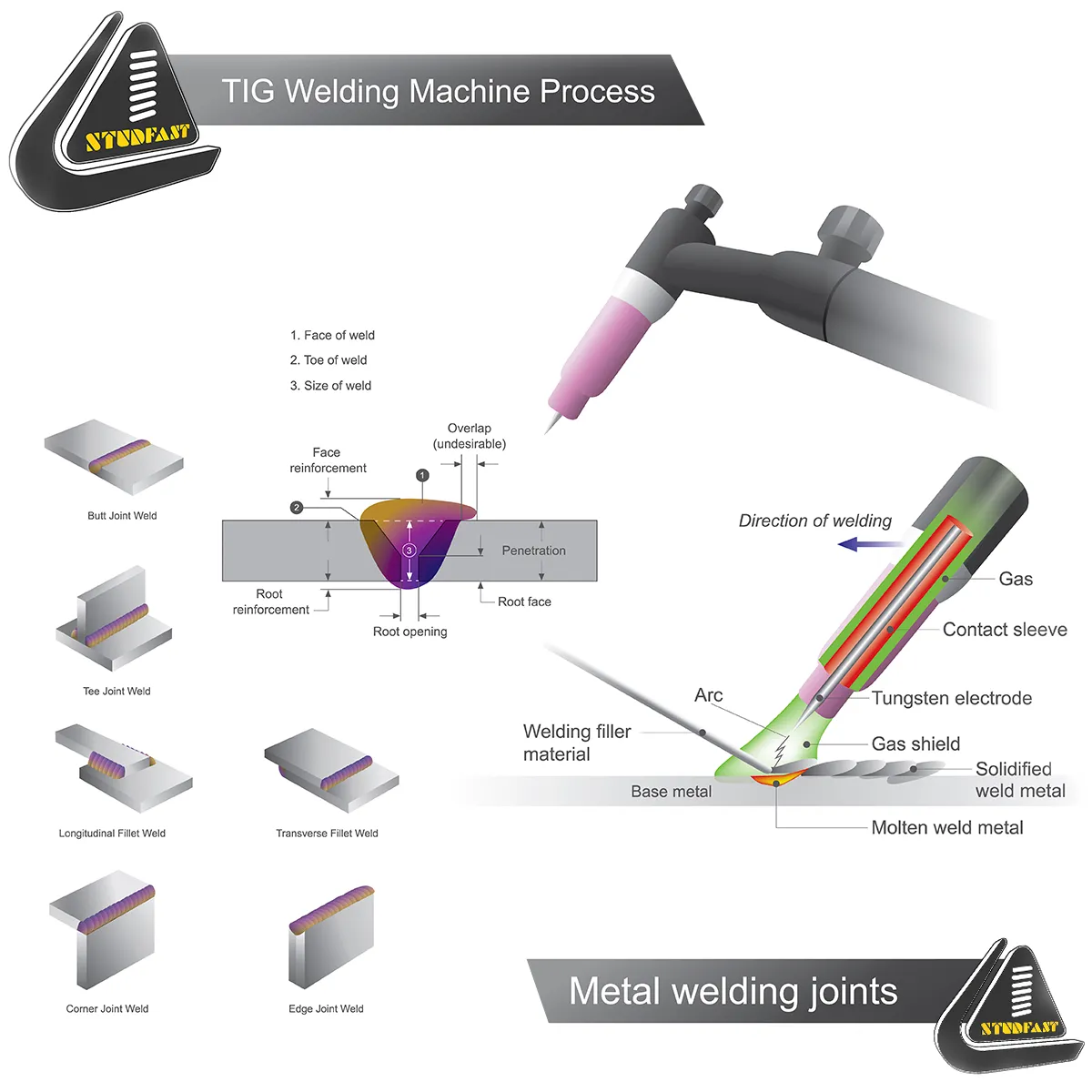
Aluminium is a lightweight material compared to steel. In applications where weight reduction is important, such as in automotive or aerospace industries, aluminium studs can help reduce the overall weight of the structure without compromising strength or performance. Aluminium is an excellent conductor of electricity. In certain applications, such as electrical or electronic systems, aluminium studs can provide efficient electrical conductivity, ensuring reliable electrical connections. aluminium has high thermal conductivity, meaning it can quickly dissipate heat. This property is beneficial in CD stud welding, as it helps prevent excessive heat buildup during the welding process, reducing the risk of distortion or damage to the workpiece.
Q: What does a metal stud welding material have in common with precious stones?
A: Inherent stability and therefore shares some corrosion resistance properties. Aluminium naturally forms a protective oxide layer that provides good resistance against corrosion. This makes aluminium studs suitable for applications where they may be exposed to moisture or corrosive environments. In fact (Studfast Fun Fact) the slightly greenish hue of the oxide that forms is actually chemically identical to sapphire. The precious stones "Sapphire" are actually comprised of crystalline aluminium oxide. And just like the precious metals, aluminium, once oxidised, is very stable and naturally corrosion resistant. Unlike our friend mild steel which we virtually always copper-flash in an attempt to coat and protect the extremely rust-prone and comparatively un-stable mucky ruddy reddish brown quickly tarnishing surface of mild steel.
Whereas aluminium has a relatively high coefficient of thermal expansion compared to steel. This can be a mixed bag of nuts when combining other materials, you want to account for this. For applications where differential expansion and contraction between the stud and the base material need to be minimised, this is advantageous, thereby reducing the risk of stress or cracking in the joint. When joining aluminium workpieces together, using aluminium studs ensures compatibility and avoids issues related to dissimilar metals. This can improve the overall performance and integrity of the welded joints. As always, for compatibility with aluminium base materials, you absolutely have to use aluminium studs. Otherwise as I've mentioned above, it's not really a 'weld' as such, but the best you can hope for is just a 'tacking on' of the stud. For some applications I've seen over the years believe it or not this has been adequate or 'fit-for-purpose', but if I'm honest, the very prospect of mis-matching materials sends a shiver down my spine and can cause me to break out in cold sweats : )